We believe there’s always a better way. That mix of ingenuity and just plain tenacity to do the right thing is how we help you make your products with the absolute highest quality, reliability and nutrition. Through vertical integration, eighteen manufacturing facilities worldwide that meet the most stringent standards, and supplier partnerships around the globe, we ensure the flexibility, responsiveness and rock-solid supply chains needed to consistently deliver the ingredients you need to make something amazing.
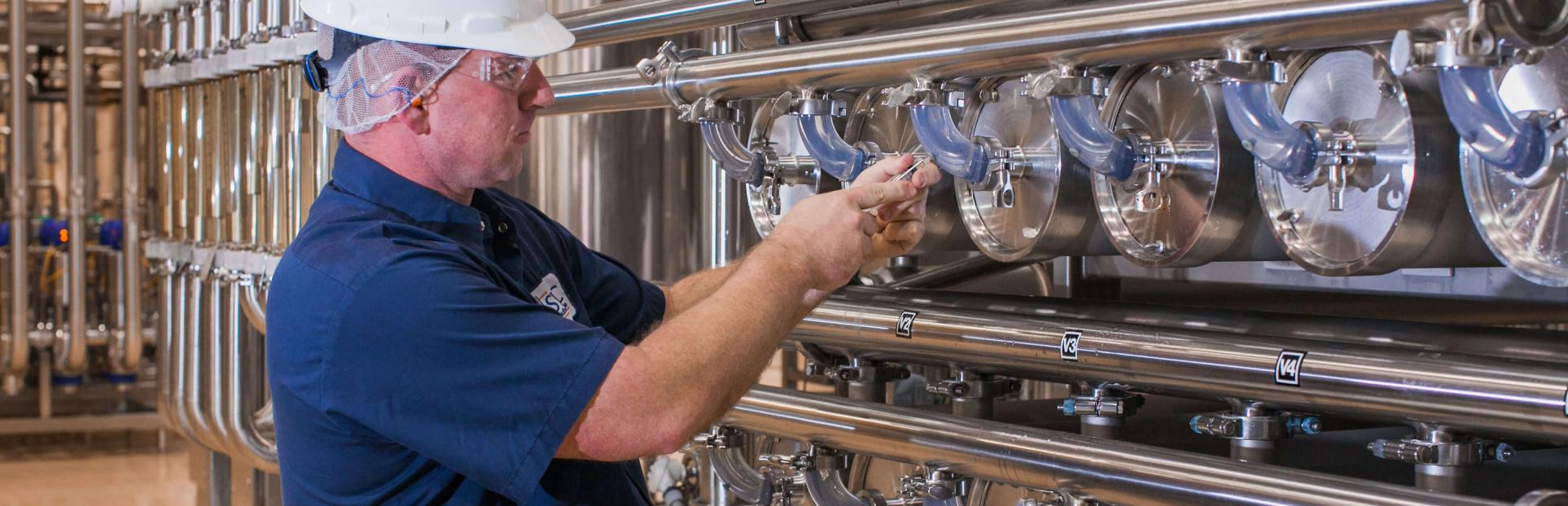
Your Glanbia
We make the highest quality nutritional ingredient and cheese solutions, at a scale & consistency you can count on.
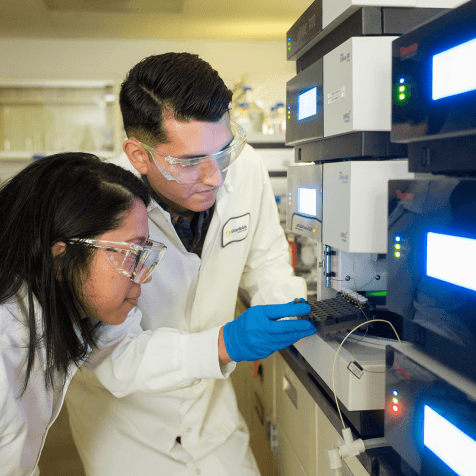
Quality
Quality isn’t just an aspect of our business, it’s at the heart of everything we do for you.
Key to that is the Glanbia Performance System. GPS is an operational platform that makes quality part of everything we do, rather than the last thing we do. From top to bottom, we apply its principles and tools to continually improve our food safety, product quality, operational efficiency and employee safety. Early management, progressive maintenance and centerlining methodologies empower operators to deal with small problems on the line, before they become big problems downstream.
Partnerships with like-minded manufacturers and suppliers help us drive quality throughout the supply chain. And failures at any scale, even near misses, drive us to find their root causes so they don’t happen again.
Together these practices are how we drive quality and safety breakthroughs throughout our operations. And they’re how we continuously earn your trust and that of some of the world’s most successful food and nutrition brands.
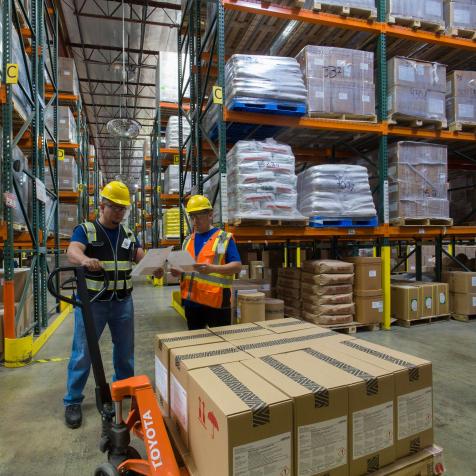
Reliability
From raw materials to finished products, we make sure everything is where it’s needed, when it’s needed.
Supply chains are the unsung heroes of manufacturing and innovation. Because even the best products don’t mean much if they’re not there when you need them. We focus on great collaboration—between operations, logistics, customers and suppliers—to keep our supply chain strong.
Our Sales team constantly aligns demand with production capacity so that when we make a promise to a customer like you, we can keep it. And we work with customers big and small to implement focused improvements that reduce losses and costs, on both sides of the table. We build close ties with the industry’s best suppliers to help keep our lines running and our customers’ inventory in stock. And we bring together a global network of third-party warehousing and distribution providers to connect every point along the supply chain—from supplier, to plant, to customer.
Supporting it all is our commitment to Total Productive Maintenance (TPM). Since 2010 we’ve continuously applied its principles to reduce material waste, eliminate equipment variation and make our operations as lean as possible. The result is one of the most valuable outcomes a business can deliver—you get what you paid for, when you expected to get it, with minimal errors. In a word, reliability.